Challenges
The apparel company had contracted with more than 400 different factories in China to manufacture and pack its products. The company spent a lot of time and resources on coordinating the factories and making sure that the right packaging reached the right factory at the right time. The quality of the packaging also varied a great deal and was often poor. The automatic handling systems in their distribution centers (DCs) suffered from low productivity due to a high number of broken boxes and a variety of sizes and designs, which required costly manual handling.
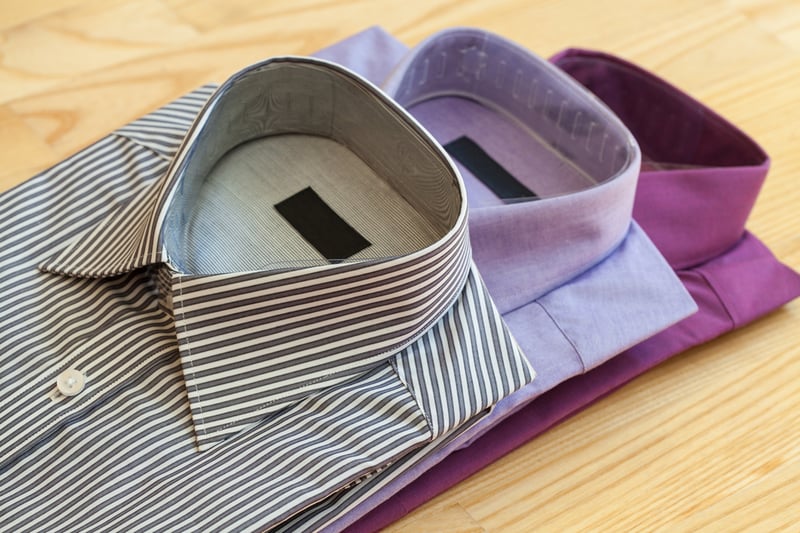
Solutions
Trillora’s technical team developed a completely new packaging portfolio of high-quality material with a uniform design that facilitated opening of the boxes at the distribution centers. Trillora was contracted to manage the entire logistics chain, from receiving the factory orders to delivery of the new packaging. We became the brand owner’s single point of contact with the factory suppliers to initiate the new packaging system and coordinate supply. We also trained the personnel at the factories to ensure successful implementation.
Results
No claims due to poor packaging have yet been reported at the importing location. 10 million boxes annually have been included in the new system and distributed from China, and today Trillora handles over 1,000 orders per week. The customer has achieved substantial operational savings: a 15% packaging cost reduction as well as indirect savings through increased efficiency at its DCs. The automatic handling now functions according to plan, with improved productivity. We ensure quality by checking that packaging specifications are maintained for every delivery, and that deliveries are on schedule.
Highlights
Optimizing apparel DC efficiencies can substantially reduce inventory and distribution costs. Financial savings can be achieved by designing apparel transport cartons that precisely meet the needs of each touch point in the carton’s journey through the DC, improve product access, meet automation needs, and drive compliance between theoretical carton size and actual carton size.